Go and See ปัจจัยสำคัญวัฒนธรรม Lean
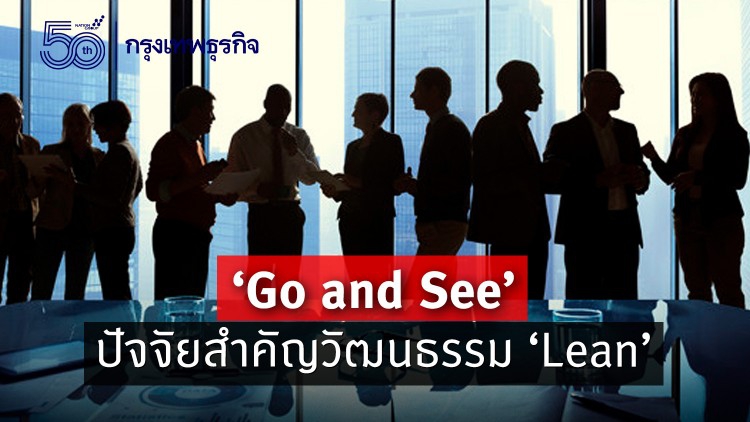
เปิดแนวคิด Go and See ปัจจัยสำคัญวัฒนธรรม Lean ที่จะทำให้ได้ข้อเท็จจริง เกิดความเห็นชอบร่วมกัน ความเชื่อถือซึ่งกันและกัน และนำไปสู่การบรรลุเป้าหมายได้อย่างราบรื่น
บทความก่อนหน้าผมได้กล่าวถึงวัฒนธรรม Lean โดยใช้ “วิถีโตโยต้า” เป็นกรณีศึกษา ใน 5 หลักการ คือ Challenge, Kaizen, Genchi Genbutsu, Respect และ Teamwork สิ่งน่าสังเกตคือ 3 ข้อแรกเป็นกลุ่มที่เกี่ยวกับ “งาน” ส่วน 2 ข้อหลังเป็นด้านของ “คน” มีสองข้อที่ใช้ภาษาญี่ปุ่นในการสื่อความหมาย คำว่า Kaizen นั้นเป็นที่รู้จักกันในวงกว้างอยู่แล้ว แต่ Genchi Genbutsu ยังไม่ได้แพร่หลายมากนัก เป็นความน่าสนใจที่ผมจะขอกล่าวถึงในบทความนี้ครับ
ความหมาย
หากแปลความตามตัวอักษรแล้ว Genchi คือ ณ สถานที่จริง และ Genbutsu คือ ของจริง เมื่อแปลเป็นภาษาอังกฤษ ไม่ได้ใช้คำตามความหมายตรงตัว แต่เลือกคำที่สื่อสารได้ง่ายกว่าคือ “Go and See” หรือ “ไปให้เห็น” สื่อความว่าการจะได้ข้อมูลที่ถูกต้องสมบูรณ์นั้น ต้องไปยังสถานที่จริงหรือต้นตอ เพื่อไปเห็นและสัมผัส ให้ได้ข้อมูลที่ถูกต้อง นำไปสู่การตัดสินใจที่ถูกต้อง
เกณฑ์รางวัลคุณภาพแห่งชาติ มีค่านิยมขององค์กรที่เป็นเลิศข้อหนึ่งในความหมายที่ใกล้เคียงกันคือ “การจัดการด้วยข้อมูลจริง” (Management by Facts) แต่ Go and See ลึกไปกว่านั้นคือการจะได้ข้อมูลหรือข้อเท็จจริง ต้องไม่ทำแค่นั่งอ่านรายงานหรือใช้สามัญสำนึกเท่านั้น ทัศนคติ คือต้องเป็นฝ่ายเข้าไปหาข้อเท็จจริงตามสภาพการทำงานจริงๆ ด้วย
ถ้าเป็นข้อมูลการผลิตในโรงงาน ต้องเข้าไปในพื้นที่ที่มีการปฏิบัติงานนั้นๆ เพื่อไปให้เห็นกระบวนการทำงานจริง เข้าใจปัญหาที่เกิดขึ้นที่หน้างาน ถ้าเป็นข้อมูลด้านการตลาดหรือลูกค้า ไม่ว่าจะเป็นลูกค้าภายนอกหรือภายใน ต้องเข้าไปสัมผัสกับลูกค้าเพื่อรับรู้ถึงความคิดเห็น ความรู้สึกและประเด็นที่จะนำมาปรับปรุงแก้ไขต่อไป สอดคล้องกับหลักการ Empathy ตามแนวคิด Design Thinking ที่พูดถึงกันมากในปัจจุบัน
สำนวนไทยว่า ผู้บริหารบนหอคอยงาช้าง ไม่ไปสัมผัสกับคนทำงาน พื้นที่ทำงาน จึงเป็นสิ่งที่ตรงกันข้ามกับหลักการของ Genchi Genbutsu
- "Go and See" กับการแก้ปัญหา
การแก้ปัญหาอย่างเป็นระบบได้ ต้องเข้าใจทั้ง “ปัญหา” และ “กระบวนการ” ที่เกี่ยวข้อง ด้วยหลักการพื้นฐาน Go and See หลังจากนั้นจึงศึกษาวิเคราะห์เพื่อให้เข้าใจถึงสาเหตุต้นตอ (Root Cause) นำไปสู่การแก้ปัญหาได้อย่างแท้จริง หลักคิดที่ต้องยึดไว้อยู่เสมอคือ ข้อมูลเบื้องต้นที่ได้มานั้นมีทั้งส่วนที่เป็น “ข้อเท็จจริง” ที่ต้องแยกให้ออกจาก “ความคิดเห็น” หรือ "สมมติฐาน" ถ้าสิ่งที่ได้รับเบื้องต้นเป็นความคิดเห็น ต้องตั้งคำถามเพื่อหาข้อมูลสนับสนุนยืนยันว่า ความคิดเห็นนั้นเป็นข้อเท็จจริงหรือไม่ ก่อนนำไปบริหารจัดการต่อไป
วิธีการหนึ่งคือ การถามทำไมซ้ำๆ 5 ครั้ง (5 Whys) ซึ่งคำตอบเกิดจากการสังเกตเห็นสภาพการทำงาน ณ พื้นที่ปฏิบัติงาน และพูดคุยกับคนที่เกี่ยวข้อง ไม่ตั้งธงว่ารู้ดีอยู่แล้ว
ข้อความเปิดเรื่องในบทความ ผมนำมาจากคำอธิบายในคู่มือวิถีโตโยต้า ซึ่งขยายความว่านอกจาก Go and See เพื่อให้ได้ข้อเท็จจริงแล้ว ยังทำให้ได้รับความเห็นชอบร่วมกัน (Consensus) ความเชื่อถือซึ่งกันและกัน (Mutual Trust) นำไปสู่การบรรลุเป้าหมายได้อย่างราบรื่นด้วย
มีคำพูดของบุคคลสำคัญในองค์กร เช่น “คุณคาดหวังว่าจะทำงานให้สำเร็จโดยที่มือไม่สกปรกได้อย่างไร” โดย Kiichiro Toyoda ผู้ก่อตั้ง สะท้อนถึงการทำงานที่ต้องมุ่งมั่น ถึงลูกถึงคน ทุ่มเท ลงแรงอย่างเต็มที่
“ระบบการผลิตของโตโยต้าถูกสร้างขึ้นมาจากการปฏิบัติจริงในโรงงาน มากกว่านักทฤษฎีวิชาการเป็นผู้กำหนด” โดย Taiichi Ohno อดีตผู้บริหารคนสำคัญ แสดงถึงการให้ความสำคัญกับการปฏิบัติ ลองผิดลองถูก
“การประสานงานระหว่างหน่วยงานเป็นสิ่งที่สำคัญเสมอ ผมอยากให้เราทุกคนคิดถึงองค์กร มากกว่าคิดถึงแต่ตนเองเท่านั้น” โดย Eiji Toyoda อดีตประธาน ที่เน้นย้ำการทำงานเป็นทีม
ประสบการณ์ตรงเรื่องหนึ่งที่ผมได้รับรู้ในวิถี Go and See ตั้งแต่การเริ่มทำงานคือ มีเอกสารเกี่ยวกับการวางแผนควบคุมการผลิตหลายฉบับ ที่ผมต้องนำไปให้คุณ Honda ผู้จัดการโรงงานในขณะนั้นเป็นผู้อนุมัติ แต่ผมจะไม่สามารถเจอตัวคุณ Honda ในสำนักงานได้เลยในเวลา 8-10 โมง เพราะนั่นเป็นเวลาเดินสังเกตการณ์อยู่ในโรงงานทุกวัน วันละ 2 ชั่วโมง!
บทส่งท้าย
คนไทยเรามีบุคคลต้นแบบอยู่แล้ว คือ ในหลวงรัชกาลที่ 9 ด้วยพระราชกรณียกิจของพระองค์ท่านที่แสดงให้เราทุกคนได้เห็นถึงวิธีการทำงาน ที่ต้องเข้าไปสัมผัสพื้นที่ พูดคุยกับผู้เกี่ยวข้อง เพื่อหาแนวทางปฏิบัติพัฒนาที่ได้รับประโยชน์ร่วมกันอย่างยั่งยืน ดังนั้น นอกจากเป็นการสร้างความเข้มแข็งของวัฒนธรรม Lean แล้ว Go and See ยังเป็นการเดินตามรอยเบื้องพระยุคลบาท โดยการปฏิบัติจริงตามศาสตร์พระราชาด้วยครับ